First, you should consider stripping any molding smoothing any walls and at least getting the walls painted with primer BEFORE you sand the floors because it would be such a shame to ruin the floors after you spent so much time making them look good. Anything falling on the floor or paint spills will be sanded out so make the mess before sanding.
Pull out any nails or carpet tacks that you can and those that won't come out need to be sunk below the surface of the wood with a hammer and nail punch. Nails will rip through sand paper and can damage the pad of your sanding machine.
If your floors are painted or covered in glue or shellac you should consider trying to strip much of stuff off with a heat gun. This will take many hours to do. The other option is to sand the stuff off but it will gum up the sandpaper and you will spend as many hours stripping off more depth of wood than necessary and changing paper. Preparation is really the key to good looking wood floors.
There are three types of sanders. For refinishing an existing decent floor that has a few scratches you want one of those giant flat palm sanders they rent at Lowes or Home Depot. You can't do too much damage with one of these but you can't get a smooth level floor either if the boards are curved or warped.
There are rotary or disc sanders. I have never seen one but some of them double up as floor polishers. These sand with a circular motion and are a little more aggressive. Edgers are rotary sanders. I have never used a disc floor sander, only an edger and an angle grinder.
The most aggressive are drum sanders. This is a giant belt sander. You have to keep moving with one of these otherwise it will gauge your floor.
If you have more than one floor to sand and don't want to worry about pulling all-nighters to get the job done so you can return the rental equipment then you should seriously consider buying a used floor sander. We did that. The drum sander cost $650 from a rental shop. Paper for it can be bought online in packs of ten averaging around $1.50 a sheet for the coarse paper and $.95 for the fine papers. We can always sell the sander when we are done and get our money back. I also have a variable speed grinder/polisher that I bought to polish my concrete counters. I use it instead of an edger. I cut 7 inch discs from the spent drum sander paper to maximise my use of the paper and save money. I also use a palm sander for some of those hard to sand spots. Here is a picture of my arsenal.
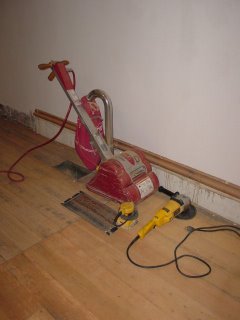
Here is a floor that I am currently working on. The left side has had a single pass with 36 grit paper.
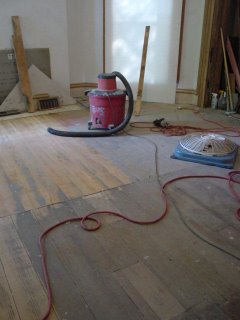
The grit size or # indicates how many "grits" there are per square inch. The higher the # the finer the paper. This floor is mostly unfinished and requires a #36, #60 and a #100 respectfully. You shouldn't need anything finer than a #100 or #120 grit for your final pass.
You should sand with the grain of the wood but you may want to make a couple of diagonal first passes if the floor is really rough or uneven. The diagonal passes cut the wood more and make levelling a much quicker process.
One end of this floor has shellac or some kind of lac paint on it. It was common to put shellac down arond the edges of area rugs. This makes sanding a messy process because it gums up the sandpaper. When this happens I get out the heat gun and start scraping. The stuff has to come off the floor and will either come off with the scraper or on the paper as a result of heat friction. Either way, the volume of goop is the same and the time taken to remove the stuff is about the same if you count the time it takes to change the sandpaper or scrape it off the sandpaper after it has cooled and hardened. In this particular case, I used the variable speed grinder to sand the remaining shellac after using the heat gun. The stuff is removed quicker if you actually allow the disc to gum up because the stuff on the floor is lifted off by sticking to the hot gooey stuff on the rotating disc. When most of the shellac was removed, I then went back to using the drum sander to do the job properly and thus reduced the amount of clogging on the drum sandpaper. Here is a picture of the problem area. The upper part is the shellac covered portion. The lower part has been sanded with both the grinder and then the drum sander with #36 grit paper.
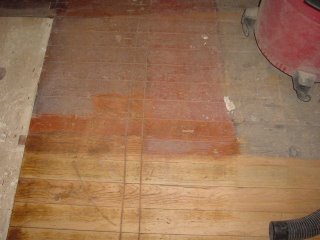
If you are using rental equipment, this kind of unforeseen hang-up will slow you down and cause much stress. The frustration could add a day to your project or make you want to pack it in altogether and put down carpet.
Once you get passed the initial removal of crud and move on to the medium and fine sandpapers it gets much easier. When using a drum sander you can lift the handle, pushing the machine into the floor to apply pressure to hard to sand patches. You can also walk very slowly almost pulling back on the machine which wants to move forward. You must keep moving though and when you get to the edge of the floor you must push down on the handle to lift the drum off the floor otherwise you will get a ridge forming along the edges of the room that will have to be sanded out with the edger or grinder. I should have this floor done in a couple of hours on Thursday now that I have scraped up the shellac and have most of that portion finished with the grinder already.
Other tips;
If you have a window fan, use it. It will get much of the finest dust out of the air and stop it from settling in your house. If all else fails, there is always laminate flooring or wall to wall carpet....
After you have done a couple of floors this process won't phase you one bit. This is my 9th floor so I get quite bored with it any more. I figured it was time to divulge the information and "spread the love" so all you folks who haven't done this yet can get down and dirty and feel my pain!